Smarter Pressure Vessel Software
COMPRESS is an expert system that produces professional level pressure vessel design reports with a single button click. It saves engineering hours while reducing errors and omissions. COMPRESS checks your inputs and makes design recommendations. This makes it the perfect solution for companies that want to bring their design work in-house. COMPRESS automates jobs that less capable solutions require you to do. Tasks such as compiling reports, determining MDMT chart assignments, calculating hillside nozzle intersections and liquid static head determinations are handled for you. Features like solid modeling, drawings, lift lugs, clips, cladding, and fatigue assessments come standard with COMPRESS.
Hightlighted Features
3D View
Nozzle pads displayed in 3D View
Nozzle pads are now displayed in the 3D View. The pad color can be changed in Set Mode Options > Options > 3D Display. [77780]
API 650
API Standard 650: Welded Tanks for Oil Storage now available
The design of Welded Tanks for Oil Storage per API Standard 650, Thirteenth Edition, is now available. See the API Storage Tank Change List for more details. [78331]
Elbows
ASME B16.9 Elbows available as main vessel components
ASME B16.9 Elbows are now available as main vessel components and may be added by selecting the B16.9 elbow icon located on the Standard Components toolbar. In addition to long radius 90 degree elbows being available, short radius 90 degree, 45 degree, increasing, and reducing elbows are also available and may be specified on the second page of the B16.9 Elbow dialog using the Elbow Type dropdown. Standard components as well as heads, covers, and custom flanges may be attached to the end of the elbow. Elbows may only be placed at the start or end of a vertical or horizontal vessel and do not permit attachments such as supports, clips, rings, nozzles, jackets, etc. directly on the elbow. [58021]
FEA-Nozzles
Finite Element Analysis for Nozzles on Cylinders
A Codeware developed FEA engine for the linear elastic analysis of nozzles in accordance with Div. 2 Part 5 and Div. 1 Appendix 46 has been implemented.
(1) Complete Div. 2 Part 5.2.2 Elastic Stress Analysis of the nozzle-to-shell junction
3D solid model based generated from COMPRESS/INSPECT model using advanced cubic Lagrangian elements
Application of Stress Classification Planes and Lines (SCP’s SCL’s) per Annex 5-A
Stress categorization of SCL results per 5.2.2.2 and Table 5.6
Comparison of linearized membrane and bending stresses to respective allowables per Figure 5.1
(2) Supported nozzle configurations:
Cylinder parent component
i. Uniform thickness, variable thickness, or long weld neck styles
ii. Set-in, set-on, or Q-lip attachments
iii. Radial, titled, or offset orientations
iv. Repads and fillet welds can be included on models
(3) New FEA Status toolbar added to home screen
Dialog provides real-time status of FEA model generation, computation, and results.
Completion status is listed including link to new HTML based interactive results. The interactive FEA model provides various plotting options including Von Mises stress, displacement, force residual, stress error, and SCP/SCL data.
i. Through-wall stress distributions are visualized via Stress Classification Planes (SCP’s)
ii. Stress Classification Lines (SCL’s) are displayed on the 3D model and SCP’s for validation and verification of results
Quick identification of load case results either passing or being overstressed without needing to perform code calculations on the entire vessel
(4) Nozzle FEA and WRC loadings dialog can be accessed from the new FEA status toolbar via the Edit Loads button
Ability to switch between either WRC-537 or FEA Load Analysis Types
A new load location option allows for the nozzle loads to be defined at either the shell-nozzle intersection point (WRC convention) or the end of the nozzle/flange surface. The loadings graphic updates based on the selection.
(5) FEA specific report for each nozzle including:
FEA model dimensions
Mesh and element type summary
Model loadings and boundary conditions
Linearized stress results for each load case and summary of governing results
Categorization of stress results as primary or secondary membrane and bending
Results images including Von Mises stress, SCP cross sectional stress, displacement, stress error, and force residual
Interactive HTML based plots are linked throughout report for quick access of in-depth results
(6) External verification of FEA model available using file export tool to save model as an Abaqus .INP input file. [78114]
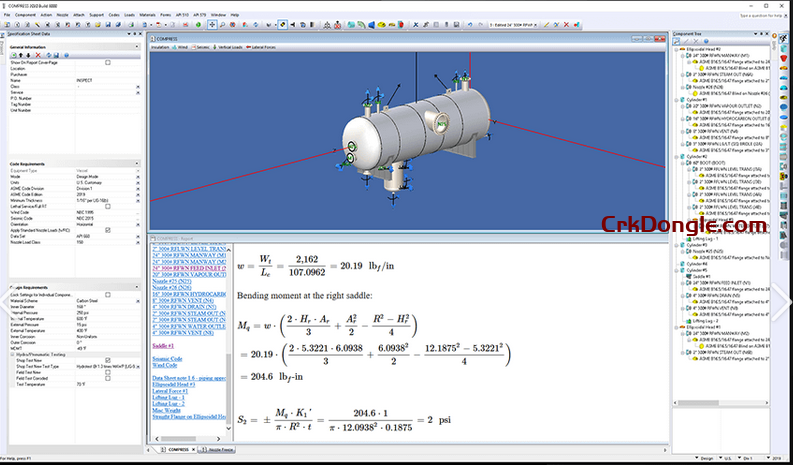